Research
Developments of Production and Recycling Processes
for Energy and Functional Materials Using Molten Salts
Development of Plating Process of Titanium by Molten Salt Electrolysis
The tungsten electrodeposition in molten salts
Production of solar-grade Si via molten salt electrolysis
Electrochemical synthesis of diamond in molten salt
Development of Plating Process of Titanium by Molten Salt Electrolysis
Titanium metal and alloys have superior properties such as high corrosion resistance, heat resistance, and specific strength. They are used for various applications of airplanes, chemical plants, sports instruments, and body implants. However, their high production cost and difficult shaping process hinder the widespread use. Plating technologies are attracted much attentions for providing their superior properties to the substrates. We are developing a new titanium plating process in molten salts that can form a homogeneous films even on the substrates with complicated shapes.
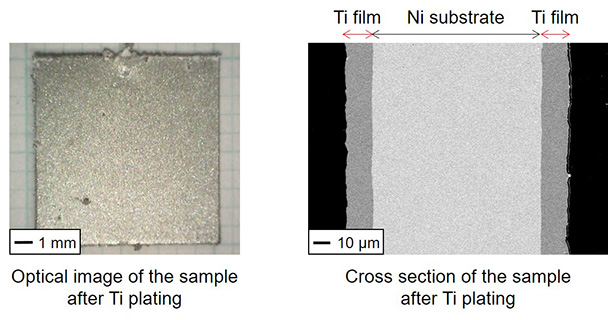
References
[1]Yutaro Norikawa, Kouji Yasuda, Toshiyuki Nohira, Journal of the Electrochemical Society, 166(14), D755–D759 (2019).
[2]Yutaro Norikawa, Kouji Yasuda, Toshiyuki Nohira, Electrochemistry, 86(2), 99–103 (2018).
The tungsten electrodeposition in molten salts
Tungsten metal has superior characteristics such as high melting point, good heat resistance, and low thermal expansion. Thus, tungsten is used for various applications such as cutting tools, filament, and heat sink. However, the use range of tungsten is limited because the processing of tungsten is difficult. If tungsten films can be plated at the metal substrates having good processability, tungsten is expected to be used more widely. We have focused on the electrodeposition in molten salts and are investigating the optimal condition to obtain high quality tungsten films.
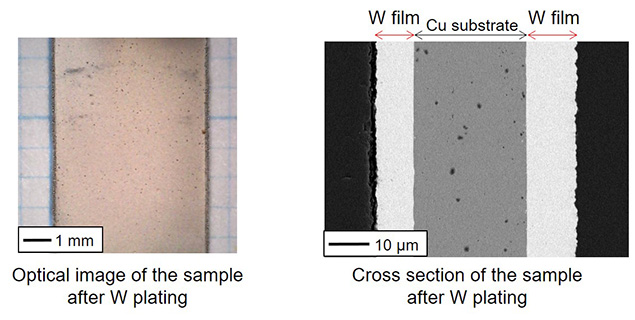
Silicon Film Formation for Solar Cells Using Molten Salt Electrolysis
Crystalline Si solar cells are currently manufactured via a slicing process into Si wafers with a thickness of 100–200 μm from Si Czochralski ingots prepared from polycrystalline Si produced in the Siemens process. A large amount of kerf loss is one of the drawbacks in the slicing process as well as the necessity of complicated multiple steps. Our research group has proposed a direct formation process of crystalline Si films on substrates based on molten salt electrolysis as a new type method of Si solar cells. We have been investigating on the quality improvement of the purity and crystallinity for the Si films, and the utilization of SiCl4 gas as a Si source.
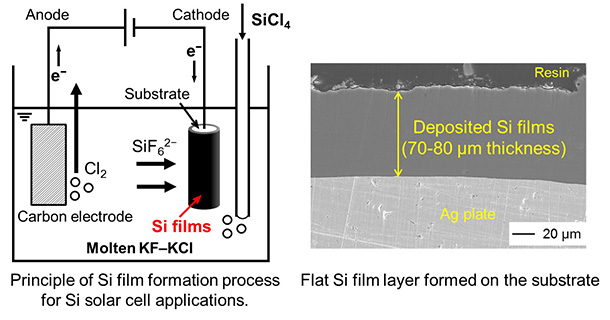
References
[1]Kouji Yasuda, Kazumi Saeki, Tomonori Kato, Rika Hagiwara, Toshiyuki Nohira, Journal of the Electrochemical Society, 165(16), 825–831 (2018).
[2]Kouji Yasuda, Kazuma Maeda, Rika Hagiwara, Takayuki Homma, Toshiyuki Nohira, Journal of the Electrochemical Society, 164(2), D67–D71 (2017).
New production process of solar-grade silicon by electrochemical reduction of SiO2 using a liquid Zn cathode in molten CaCl2
We proposed a new process using liquid Zn cathode on electrochemical reduction of SiO2 in molten CaCl2 to product solar-grade silicon. Three major steps are included: (1)Electrolysis step: SiO2 is electrochemical reduced as silicon and composed liquid Si–Zn alloy, (2) Precipitation step: Solid silicon is precipitated when lowering the liquid Si–Zn alloy’s temperature from 1123 K to 923 K, and (3)Refining step: Volatilize Zn from Si and product solar-grade silicon ingot by directional solidification. The recovery of silicon from the cell and the separation of silicon from SiO2 and molten salt is easy because silicon is recovered as liquid Si–Zn alloy. Besides, effective removal of impurities is expected when silicon is precipitated from liquid Si–Zn alloy.
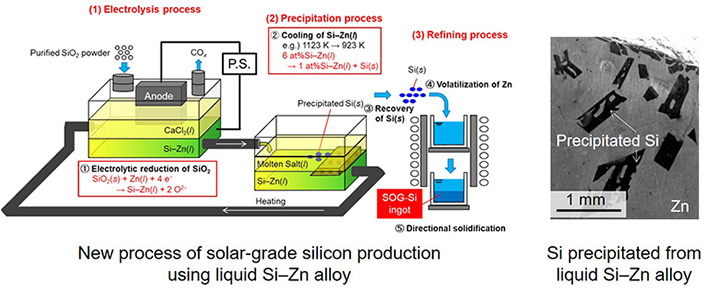
References [1]Kouji Yasuda, Takeyuki Shimao, Rika Hagiwara, Takayuki Homma, Toshiyuki Nohira, Journal of the Electrochemical Society, 164(8), H5049–H5056 (2017). [2]Yuanja Ma, Akifumi Ido, Kouji Yasuda, Rika Hagiwara, Takayuki Homma, Toshiyuki Nohira, Journal of the Electrochemical Society, 166(6), D162–D167 (2019).
A new recycling process for RE metals from scrap magnets using a molten salt electrochemical process and an alloy diaphragm
A Dy–Nd–Fe–B magnet is utilized in many important applications such as high-performance motors for electric vehicles. However, heavy RE metals such as Dy are difficult to supply stably. Thus, it is necessary to develop an efficient recycling process for RE metals. We have proposed a new recycling process for RE metals from magnet scraps using a molten salt electrochemical process and an alloy diaphragm. We are developing new diaphragm materials which have higher durability compared to the conventional Ni.
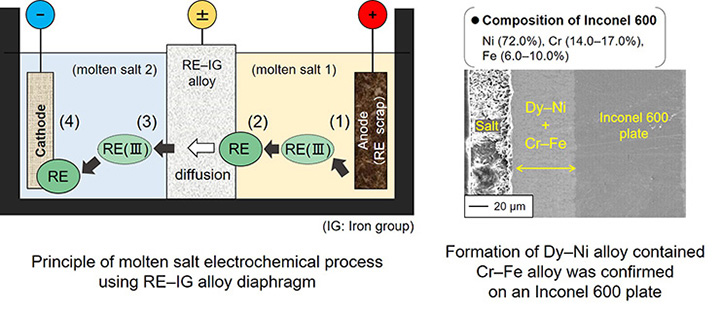
Electrochemical synthesis of diamond in molten salt
Since diamond has many superior properties, diamond is expected to utilize as not only jewelry but materials; cutting machine and semiconductor. However, currently there are problems that the amount of product of natural diamond is too little and artificial diamond synthesized by conventional methods is too expensive. In order to resolve this situation, we research to develop the completely new synthesis method which is electrochemical deposition of diamond in molten salt under ambient pressure.
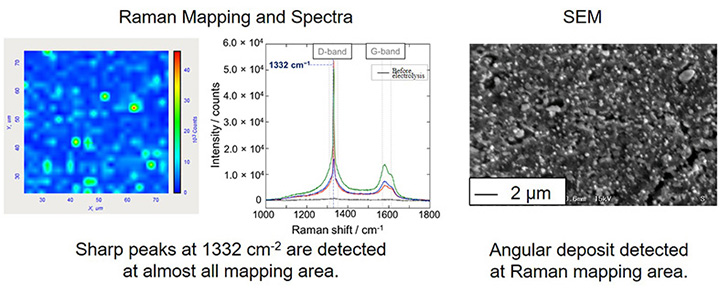
Development of new rechargeable batteries
using ionic liquid electrolytes
Renewable energy resources such as solar and wind power are intermittent resources, and their electric power generation are largely dependent on weather. Thus, widespread introduction of these energy resources may lead to a serious problem of unstable power supply. One promising solution is the wider distribution of large-scale batteries in households, buildings, industrial plants, etc. Current lithium-ion batteries are candidates for large-scaled batteries, but scarce resources (lithium, cobalt) and flammable electrolytes (organic solvents) are used as main components, which might be a major barrier to the further distribution in the future.Our group has focused on next-generation batteries utilizing abundant resources (sodium, potassium, etc.) and safer electrolytes (ionic liquids). Ionic liquids possess high safety such as negligible volatility and nonflammability. As shown in the figure below, a prototype of potassium secondary batteries can be constructed by combining ionic liquid electrolytes with potassium-based layer compounds as positive electrodes and carbonaceous negative electrodes. We have developed several ionic liquid electrolytes for potassium secondary battery, and now we investigate charge–discharge performance of various electrode materials to construct prototype batteries with ionic liquid electrolytes.
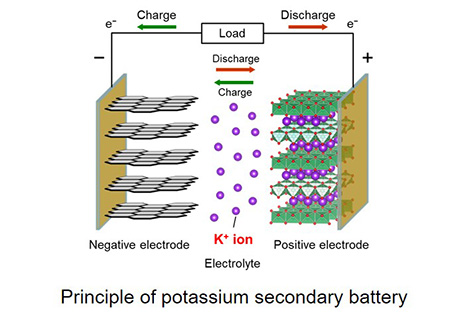
References [1]T. Yamamoto, K. Matsumoto, R. Hagiwara, T. Nohira, The Journal of Physical Chemistry C, 121, 18450–18458 (2017). [2]T. Yamamoto, T. Nohira, Chemical Communications, 56, 2538–2541 (2020).
Highly Efficient Water Electrolysis Using Hydrate Melts
There is great anticipation for a "hydrogen energy system" that converts surplus renewable energy into green hydrogen through water electrolysis, stores and transports it, and then converts it back into electricity using fuel cells or hydrogen turbines. To respond to the full-scale introduction of renewable energy, it is important to improve the energy efficiency of water electrolysis. We are developing a highly efficient water electrolysis method using hydrate melt electrolytes, which are characterized by significantly lower water contents than ordinary aqueous solutions.

References [1] K. Kawaguchi, K. Goto, A. Konno, and T. Nohira, J. Electrochem. Soc., 170, 084507 (2023). [2] K. Goto, K. Kawaguchi, and T. Nohira, Electrochemistry, 92, 043021 (2024).